WHY TEST MOTORS FOR CORE LOSS?
- Zlatko Tušla
- Apr 17, 2021
- 2 min read
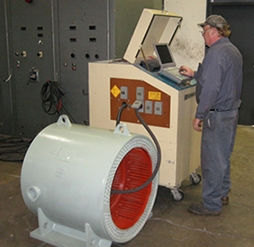
Core loss testing has become essential in ensuring quality electric motor and generator repairs and should be a standard procedure at any rewind shop. When rewinding motors, this testing is a vital step for corrective maintenance.
It's well known that core loss is second only to copper loss in motor windings in causing motor inefficiency
Core loss is the major cause of wasted electrical energy which can result from overheating during operation, motor burnout, and physical damage such as rotor drag. Defective bearings, the most common cause of electric motor failure, often results in core damage. A damaged core will lead to a winding failure .
Core Testing should be performed prior to removing the old windings to determine whether or not the iron core is damaged .
After the windings are removed, the core is retested to be sure that any damage didn’t occur in your rewind shop while heating and removing the old winding.
Two issues arise when roasting a stator core:
the core losses increase which makes the motor run hotter and less efficient.
the hot spots appears, which will shorten the insulation life, thereby reducing the life span ie. meantime between the failures.
If damaged, the motor could run hot and motor lifespan will be greatly reduced. The motor will generate more heat since it will consume more power to operate normally.
The tester indicates the condition of iron-core by measuring the watts of energy lost per kg when the core is excited to operating conditions. Additionally, the infrared heat camera can record “hot spots” in the stator. These are caused by physical contact between rotating parts and the core as well as “grounds” where the winding have arced and blown holes in the iron-core.
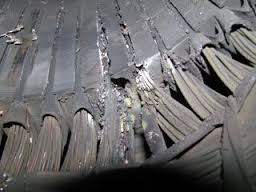
The tester indicates a allowed range in terms of flux, watts, and amps. If the core does not meet a minimum value, the steel lamination making up the core must be repaired, restacked, or replaced.
Without this testing, it is impossible to determine that a motor is capable of operating at rated efficiency after rebuilding.

Motors that have failed and are not core tested often experience repeat failures.
Motors should be tested and a printout of results provided to the customer.
BTW, manufacturers of core loss testers are invited to contact us with detailed information on their benefits and how to use their tester. Any useful instructions will be published on this site.
Comments