Rewind or Replace
- Zlatko Tušla
- Apr 17, 2021
- 3 min read
Generally, rewinding can produce a motor with the same efficiency it had when it was new, but in reality, the quality of a motor rewind, and hence the impact on efficiency, is highly variable; and depends on the materials and techniques used in reassembling the motor.
The majority of motors sent to repairers can be repaired satisfactorily. However there will be some which have suffered irreversible damage and which even if rewound will not run for very long before further failure occurs. These motors will certainly run at reduced efficiency.
The estimated increases in energy loss after repair range from 2.8% to 6.1%.
When such a motor is received for repair, a replacement should be considered.

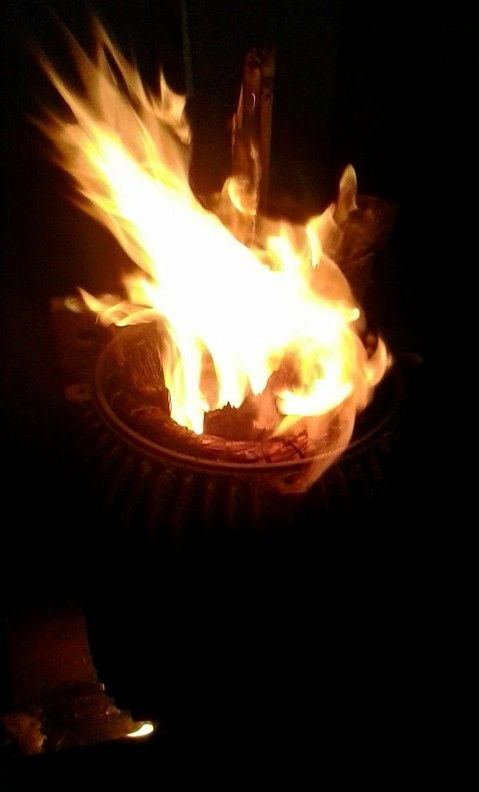
Before a stator core can be rewound, the original windings must be removed. There are various ways of doing this. Many motors — especially those in which the windings are just laced in place — can be easily “dry stripped” or “cold stripped.” Here, the ends of the windings are cut off and the wires within the slots are simply pushed out.
Where dry stripping is impractical, there are another alternatives.
1). Cutting off one endwinding In some rewind shops this is done by hand using a hammer and chisel which renders the stator core liable to damage if the chisel slips. Such physical damage could result in iron loss increase and efficiency decrease. The best method of cutting off one endwinding is to use a jig located circular saw. This method also has the advantage of being much quicker as well as safer. Hydraulical coil pulling machine for stators and rotors is shown:

2). Releasing the varnish from the old winding In some small motors it is possible to remove the winding without pre-heating but in most cases some heat is applied to soften the varnish which is used as part of the winding insulation system. Other methods of varnish release (eg chemical) have become less common because of environmental issues. Heating the windings inevitably results in some heat being transmitted to the stator core. As a general rule, if stator cores are heated to more than 300°C (360°C for smaller motors up to about 30 kW) some damage may occur to the interlaminar insulation.
There are three methods generally used for heating: • Hand held torch (usually propane , natural gas or acetylene) • Heating table • Burnout oven with controlled temperature
• Hand held torch

The hand held torch with the flame directed on to the remaining endwinding is both the cheapest and on small motors the quickest method of heating the insulation prior to removing the windings.
Its use on large motors (say above 55 kW) is less common because the heat output of the torch is often unable to get all the winding warm in a reasonable time.
This process is completely under the control of the operator ( must be an experienced operator who has received appropriate training) and if the torch flame is accidentally allowed to play directly on to the core it can quickly damage the interlaminar insulation.
This kind of demage will decrease the motor efficiency.
It is very difficult to perform this procedure without damaging the core. That's why we can not recommend this method at all. Moreover, our recommendation is to avoid all service centers with such a practice. After such a "treatment" ( shown on the photo), usually the motor is on the right way to scrap yard.
• Heating table
Heating table is fixture in which stator is held into a vertical position with the remaining endwinding pointed downwords or upwards. The gas jet is directed on the endwinding that allows the heat is transferred through the copper wires in the slot. Note that thermal insulating shield, placed around the slots, must be used in order to prevent direct heating of iron-core.
Usually, this king of heating table is combined with a winding puller above mentioned.
This method is not an expensive option and it is recommended.
• Burnout oven with controlled temperature
Burnout oven with controlled temperature is best and most expensive option. They are widely used in the repair shops despite the fact that this method requires more time and it is not energy efficient if not maximally loaded
Comments